Adding Textures to Wood
Gareth's Tips, Tools, and Shop Tales - Issue #79
I am still looking for tips testers: Pick a tip (any tip), subject it to honest, real-world testing, report back. 3 tipsters will win signed copies of my Tips and Tales from the Workshop Volumes 1 and 2 (V2 coming this spring).
Adding Textures to Wood
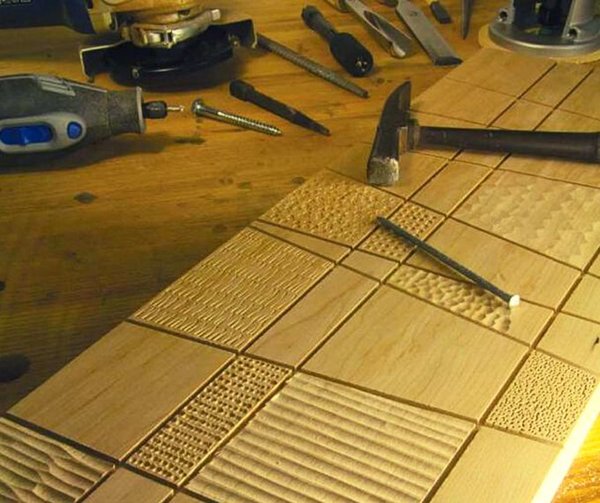
So many cool textures with common tools and materials.
Make: tweeted a link to this piece I did on their website many years ago. Apparently it still gets a lot of traffic. Looking at it again, I see why. Lots of great ideas in here (from Canadian Woodworking) on using screws, round files, chisels, and other tools and hardware to create patterns/textures in wood.
Saving the Best for Last
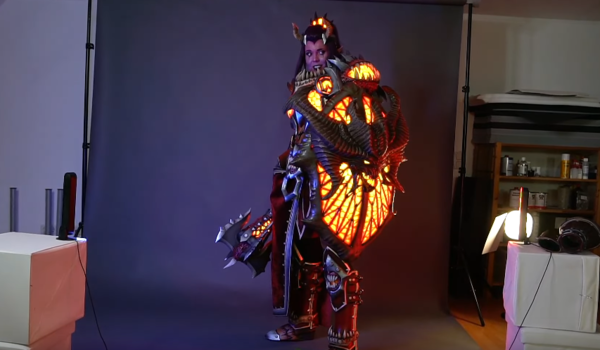
A year and a half in the making!
On KamuiCosplay, Svetlana shows off the amazing “Demonic Brigitte” outfit she spent a year and a half working on. In the video, she shares a great tip: When doing a long and complicated project, don’t be tempted to build the part that you’re most excited about first. Save it for the end. That way, it’ll power you through the less exciting parts. In her case, she was most excited about making the shield, so she saved that for last.
Making a Disposable Utility Knife with Leftover Resin
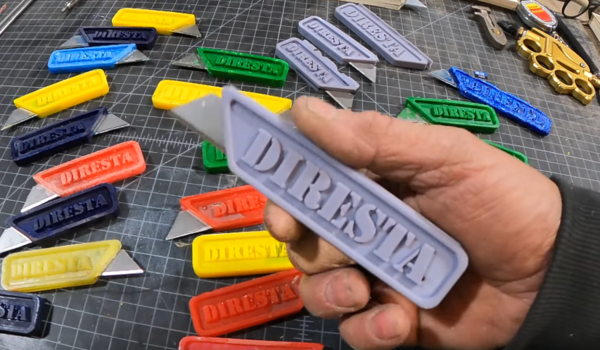
Can’t have enough of these around home and shop.
Jimmy DiResta had a cool idea. He created a mold for a disposable utility knife, so if he’s casting something and has a bunch of leftover resin, he can cast a disposable utility knife with the excess. He’s planning on developing the mold into a product for sale, but you could obviously create such a mold yourself. This project also raises a question. If you do a lot of casting and have leftover resin, what other tools and castable objects can you create silicone molds for?
Cable Organizing and Labeling
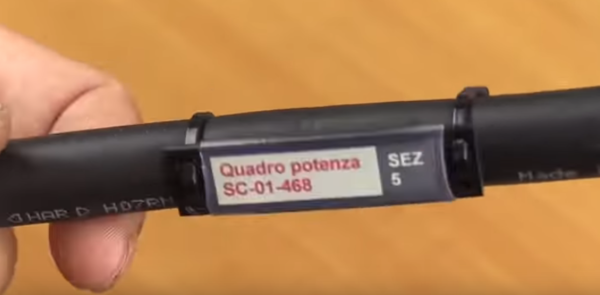
“Cable labeling” Say that 20 times!
To be honest, I found this video annoyingly redundant. But it was a good reminder of how you can use plastic cable ties to neatly organize cable runs and pieces of ties and clear heat shrink tubing for creating handsome cable labels.
Inverting Boxes
Do you have some cardboard boxes that are downright grotty from multiple trips through the mail system or new shipping boxes from mailing services you no longer use? Hopefully, you already know this, but you can easily turn those boxes inside out and give them a new life. I used to use FedEx years ago and had a big stash of their boxes in every size. Now, I just invert them to mail through other services. [Via Jimmy DiResta]
Shop Tales: Beewax and Boning
Back in October, I got this wonderful email from reader Jeff B, in response to my call for shop tales I can use in the next volume of my tips book. This is exactly the sort of thing I’m looking for. Thanks, Jeff!
In the mid-1980s, I lived with my wife and two kids in Seattle on the south side of Queen Anne Hill. I worked at a funeral home at the time and walked two miles to work. I made myself a walking stick from a piece of driftwood and sealed it with shellac, or something similar. Several times during my daily walking commute, I ran into Mr. Ball (that’s all I ever knew him as). He was about 70, spoke with a southern accent, and always wore a suit and tie. He used a walking stick, too, of his own making. His was curly willow, with sinuous twists to it. Mr. Ball chose a walking stick with a natural fork in it. The bottom third of the stick had two legs leaving the fork, and each leg was a curly mirror image of the other. At the bottom of the stick, Mr. Ball put two plastic champagne corks to protect the wood. He looked at my stick and suggested that I use something more natural and less toxic to seal future walking sticks. He used beeswax, rubbing it into the pores of the wood with a piece of bone or antler. He called this boning. He said it also compresses the outer layer of wood, making the surface stronger. After the boning, you go over the wood with a cloth to make the wax shine. Mr. Ball also said that as a child he didn’t have sandpaper. He’d smooth wood by using a piece of broken glass.
We moved and I never saw Mr. Ball again. I often wonder about him. I’ve used the beeswax and boning method on dozens of projects since. Next to my workbench, I have a little cardboard box of beeswax, a few antler sections, and a piece of bone.
02/11/21(Gareth’s Tips, Tools, and Shop Tales is published by Cool Tools Lab. To receive the newsletter a week early, sign up here. — editors)