Maker Update: Hakko CHP-170 Flush Cutter
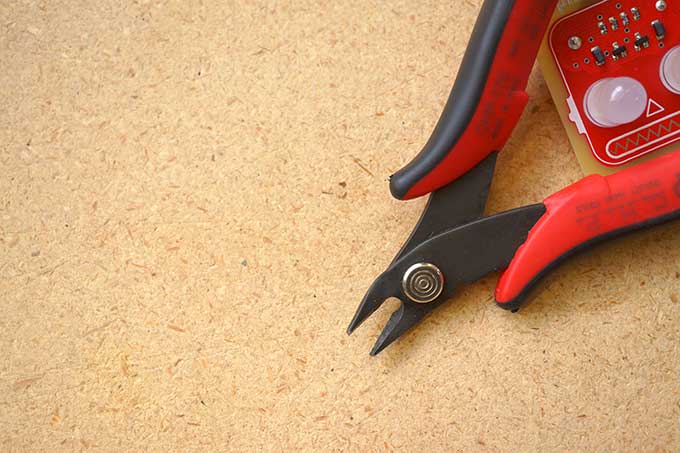
Trims component wires completely flush to surface
This week on Maker Update, an enchanted talking tiki totem pole, my trip to OSH Park and Metrix Makerspace, a retro lightbox, and why you need flush cutters. This week’s Cool Tool is the Hakko CHP-170 Flush Cutter.
This time around I’m going to show you my favorite pair of flush cutters for electronics. They’re just $5 on Amazon, and made by Hakko. By picking these using the link in the description you help to support my show and the Cool Tools blog.
For more years than I care to admit, I would cut and trim wires and circuit leads using these generic wire cutters. They’d get the job done, but because the blades are somewhat recessed, you could never trim things completely flat.
For that, you need flush cutters. And it’s a subtle distinction, but these are so much more satisfying when you’re cleaning up the bits of wire on a project. Because the cutting edge is moved all the way out front, you can take the cut right down to the board if you want.
And here’s a quick tip. I learned this from watching how Saar Drimmer from Boldport solder up his beautiful projects.
Typically, when you solder a connection together on a through-hole circuit board like this, you get what looks like a mountain of solder. You come back through and trim it down, and maybe you get something like this, and it’s tidy and gets the job done.
But these days, with project boards that are almost works of art in themselves, here’s a technique for making solder joints that are prettier and smoother to touch.
Take that same joint you just made, and use flush cutters like these $5 Hakkos to trim the joint right down to the board.
Then, come back around with your soldering iron, reheat the connection very quickly and hit it with a touch of solder.
It takes some practice, but if you get it right, you get a perfect little dome. Something about the surface tension of the new solder and the lack of any central element poking through makes this happen.
And when you apply this technique to an entire board, it almost looks like it’s been put together with little rivets. It’s a nice look and it’s smooth to touch. Clean up the extra flux with a swab of isopropyl alcohol, and you’ve got a board worth showing off.
You don’t need any special soldering iron or solder to make this technique work, but you really do need the flush cutters to get right up against the board.
09/7/17Hakko CHP-170 Micro Soft Wire Cutter ($5)