Jordan Bunker, Former Tech Editor for Make:
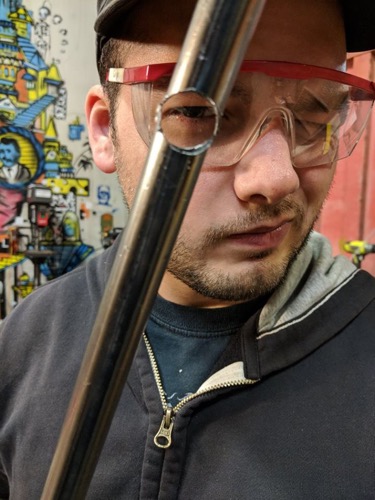
Cool Tools Show 189: Jordan Bunker
Our guest this week is Jordan Bunker. Jordan is a freelance engineer, designer, artist, and prop-maker based out of Oakland, California. He’s also a former Make: magazine technical editor and BattleBots robot builder. You can find him on Twitter and Instagram at @TensorFlux.
Subscribe to the Cool Tools Show on iTunes | RSS | Transcript | Download MP3 | See all the Cool Tools Show posts on a single page
Show notes:
Dykem Steel Blue Layout Fluid Spray ($14)
When working with metals, it’s useful to be able to make clear, precise lines on the surface to be worked on. Layout fluid is typically applied to the surface and allowed to dry as a colored film, and then a scribe is used to make light marks in the film. Many home-shop machinists know about the brush-applicator type of fluid, but this particular product is a spray, which makes applying the fluid a lot faster. There’s lots of different companies that make layout fluid, but Dykem is kind of the go to company for a lot of machinists and fabricators. I typically use blue or red. I think it’s just easier to see things in blue and red.
McMaster-Carr Catalog
MCMaster Carr is one of my go-to companies for just about any kind of material or hardware needed for a project. Of course, you can search for what you need on their website, but being able to physically page through their catalog can often reveal the existence of hardware that you didn’t even know existed. They only make a limited number of these catalogs, and they aren’t available for purchase on their website, but I’ve heard that if you order often enough from them, they’ll send you one. You can also request one from them, but I’ve never tried, and I find it’s easier just to buy one from eBay for about $30 or $40. It’s not color. Everything’s in black and white, but there’s a photo — I mean, they’re actually beautiful illustrations. I’m not sure how they exactly they’re generating, they look like kind of like their photos that they’ve converted to line drawings, but everything’s in black and white. Mine’s actually doubled as a coffee table book, just because I find it so useful.
Air Force Jumpsuit (used, varies)
In my shop, I do a lot of welding, grinding, and working with chemicals. I found that I needed some kind of covering that would protect me, and found that military jumpsuits are a great option. Our tax dollars went into developing these suits, and they manufacture them by the thousands, so they’re easy to get ahold of online or at a military surplus store, typically for about $20 – $30. They come in a variety of sizes (just as recruits do), and are made of a temperature-resistant, chemical-resistant, and abrasion-resistant material. I’ve been using mine for years, and have yet to put a hole in them (unlike several of my shirts and jeans). What you want to look for is Aramid fabrics. It’s kind of a class of fabrics or fiber — Kevlar is one of them, Nomex is another, they’re kind of brand names — but they’re specifically formulated to be temperature, chemical and abrasion resistant.
Hot Air Rework Station ($55)
Most of the prototyping I do requires electronic design as well, and if you’re working with surface mount components, a hot air station is pretty vital. Usually when people think of soldering, they think of a soldering iron and that’s great for what are called through-hole components. Well, if you’re doing anything surface mount where there are no holes in the board, you’re just sticking a component right onto the surface, and getting your soldering iron right there is a little tricky. So, a hot air station, what it does is it blows hot air out of the tip of this sort of wand and directly onto your parts and kind of melts all of the solder right around the area where it’s heating up. So that’s really useful if you’re doing very small surface mount parts. And a lot of times if you go to look for a hot air station, they can be pretty expensive. A lot of them have lots of fancy bells and whistles and you’re paying two or 300 bucks for these things. But this model is around $40 and doesn’t really have any fancy options or anything like that. You can dial up the temperature and you can change the air pressure — the force of the air blowing out. But it’s great to have it on the bench, Even if all you do use it for heat shrink tubing, which is where mine gets most of its use.
Also mentioned:
Make: magazine Skill Builder Articles
I recently moved to San Francisco to work for Make Magazine, as a technical editor. And one of the things that they wanted me to kind of exclusively write about was kind of just sharing all the random knowledge I’ve accrued over the years of different materials and processes, and how to work with them. So the Skill Builder articles, we’re kind of focused on some things that are very simple, like how to use hand files appropriately. Most people don’t realize there’s two different techniques. There’s the one where you kind of a draw your file along parallel to the thing that you’re filing, but there’s also the way where you turn it perpendicular and you kind of scrub it across the surface and it results in a lot finer shavings, so you can smooth things out a lot better. There’s all sorts of little tips and tricks for how to work with acrylic or I did a whole section on different types of rivets. I also went into how different technologies work. Like with lasers — there’s big gas tube lasers that you might be familiar with, if you worked with a laser cutter before — but you know how do those laser pens work? How is it generating the light? Those sorts of things. So the Skill Builder series of articles was really just to kind of give people the groundwork. Because a lot of times you’ll buy files, but they don’t come with an instruction manual. And if you try to look it up online, there’s all sorts of information. It kind of just feels like drinking from the fire hose. So I was trying to provide a very simple way for people to kind of get their feet wet and learn slowly about all the different ways to interact with materials and use the tools that they might have in their shop.
We have hired professional editors to help create our weekly podcasts and video reviews. So far, Cool Tools listeners have pledged $390 a month. Please consider supporting us on Patreon. We have great rewards for people who contribute! If you would like to make a one-time donation, you can do so using this link: https://paypal.me/cooltools.– MF
08/23/19